Electric Tube Cutters: Types & Uses for 2024
As industries continue to evolve and strive for more sophisticated manufacturing and production techniques, precision equipment like electric tube cutters become invaluable. Clean Room Devices, a notable company in this arena, offers a variety of electric tube cutters designed for high precision and clean operation, ideal for industries where contamination is a concern, such as biomedicine, pharmaceuticals, and semiconductor manufacturing.
Significance of Electric Tube Cutters
Electric tube cutters excel in precision cutting, ensuring that every piece of tubing meets exact specifications. This precision is critical in applications where the integrity of the tube’s edges and the cleanliness of the cut can directly impact product quality and functionality. Clean Room Devices designs its cutters with these high standards in mind, ensuring that they meet both the operational needs and the regulatory requirements of clean room environments.
Features of Top Electric Tube Cutters
- Precision and Speed: Designed to deliver quick and accurate cuts that meet stringent industry standards.
- Clean Room Compatibility: Constructed with materials that prevent contamination, crucial in clean room settings.
- Versatility: Able to handle a variety of materials, including different types of plastics and composites, accommodating diverse industrial needs.
Exploring Clean Room Devices’ Electric Tube Cutters
CRD100 Tubing Cutter
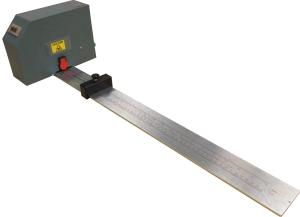
The CRD100 Tubing Cutter is an adaptable tool, cutting tubing sizes from 1/16″ to 1/2″ OD. This device is designed for clean rooms, ensuring that operations remain contaminant-free. It’s perfect for precision cutting required in medical tubing and small-component manufacturing.
Large Electro-Pneumatic Cutters (CRD180 Series)
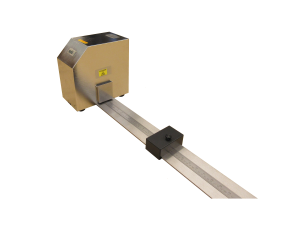
For larger tubing, the CRD180 series can handle diameters from 1/2″ to 1-1/2″ OD. This series is particularly effective in high-volume environments where larger diameter tubes are common, such as in industrial applications and heavy machinery.
CRD190 60° V-Notch Tubing Cutter
Specializing in V-notch cuts, the CRD190 is ideal for specialized medical applications where a specific type of notch is required. This could include custom manufacturing of components where angular or notched cuts are necessary for the assembly of complex devices.
CRD170 Multi-Angle Tubing Cutter
Offering the capability to cut at various angles from 15° to 90°, the CRD170 is exceptionally versatile. It supports precise angle cuts needed in intricate designs and configurations, vital for aerospace, automotive, and sophisticated electronic device manufacturing.
Industry Applications
The applications of these cutters are extensive and diverse:
- Medical Manufacturing: Used in creating critical medical device components like catheters and surgical tools which require precise dimensions for proper function.
- Pharmaceutical Production: Ensures the accurate cutting of tubes used in drug delivery systems, where dosage and delivery method must be exact with certain requirements to the cleanroom environment.
- Semiconductor Manufacturing: In the production of semiconductors, precise and clean cuts are necessary to ensure the integrity of the chips and circuits.
- Laboratory Settings: Research and development labs utilize these cutters for preparing specimens and components in experiments and tests.
The Future of Electric Tube Cutting
As we continue in 2024, advancements are expected to center on increasing automation, enhancing precision, and improving the user interface of these devices. Developments may include more sophisticated digital controls, automated feeding systems, and advanced diagnostics to monitor wear and operation in real-time. These improvements will likely drive greater productivity and ensure that electric tube cutters can meet the increasingly sophisticated demands of industries reliant on precision fabrication.
In addition, environmental considerations and sustainability are becoming crucial in manufacturing decisions. Future electric tube cutters might incorporate more energy-efficient designs and use materials that are easier to recycle, reflecting the growing trend towards greener manufacturing practices.
Conclusion
Electric tube cutters are more than just tools; they are integral components of modern manufacturing, ensuring that industries like medical device production and semiconductor manufacturing meet their rigorous standards. Clean Room Devices continues to innovate in this field, providing cutting-edge solutions that meet the needs of various high-tech industries. As we continue in 2024 and beyond, the role of these tools will only grow, underscoring their importance in achieving the precision and cleanliness required in critical manufacturing processes.