Advanced Fitting Inserters: Enhancing Cleanroom Efficiency
In the realm of cleanroom operations, precision and efficiency are paramount. One of the critical components ensuring smooth operations in these controlled environments is the fitting inserter. At Clean Room Devices, we specialize in providing advanced fitting inserters designed to meet the rigorous demands of various industries, including medical device manufacturing, automotive, and more. This blog will delve into the importance of fitting inserters, the types we offer, and how they can enhance cleanroom efficiency.
Understanding Fitting Inserters
Fitting inserters are essential tools in cleanrooms, particularly where precision is crucial. These devices facilitate the quick and accurate installation of flexible tubing, which is a common requirement in many manufacturing processes. Automating this process significantly reduces manual labor, improves accuracy, and enhances overall productivity.
Types of Fitting Inserters at Clean Room Devices
At Clean Room Devices, we offer a range of fitting inserters tailored to different needs and applications. Our product line includes both semi-automatic and manual, each designed to address specific operational requirements.
Semi-Automatic Fitting Inserters
Semi-automatic fitting inserters strike a balance between automation and manual operation. These devices are ideal for high-volume production lines where speed and precision are critical.
Features and Benefits:
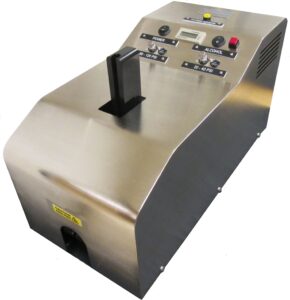
- Efficiency: Semi-automatic significantly reduces the time required for installations. Operators can quickly position tubing and the machine takes over the insertion process.
- Precision: These inserters ensure consistent and accurate installations, reducing the risk of errors that can occur with manual processes.
- Ergonomics: Designed with operator comfort in mind, semi-automatic minimizes repetitive strain injuries, which are common in manual operations.
- Versatility: Our semi-automatic, like the CRD400, can accommodate a variety of tubing sizes and geometries, making them suitable for diverse applications.
Manual Fitting Inserters
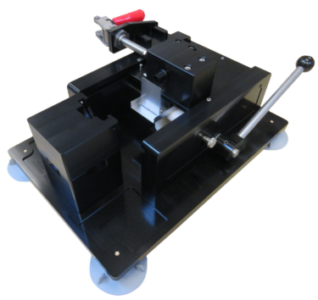
Manual fitting inserters are perfect for applications where flexibility and control are paramount. These devices offer hands-on operation, allowing operators to manage each step of the insertion process.
Features and Benefits:
- Control: Manual ones provide operators with complete control over the process, making them ideal for intricate or custom applications where precision handling is required.
- Flexibility: These inserters can be easily adapted to different types of tubing, offering versatility for various tasks.
- Cost-Effective: Manual inserters are often more affordable than their semi-automatic counterparts, making them a cost-effective solution for smaller operations or specialized tasks.
Highlighting Our Product Range
CRD400 Semi-Automatic Fitting Inserter
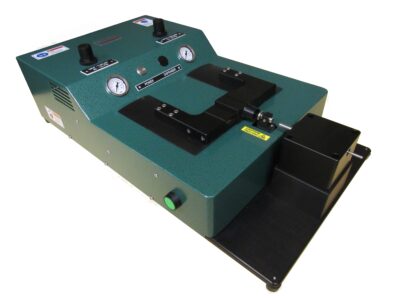
The CRD400 is one of our flagship semi-automatic, designed for high-volume production lines. This inserter is equipped with features that enhance its performance and reliability.
Key Features:
- Rotating Nest: The CRD400 includes a rotating nest for multi-barb fittings, allowing for precise and secure fitting installations.
- CE Certified: This model meets stringent CE certification standards, ensuring safety and reliability in cleanroom environments.
- Adjustable: It accommodates tubing from 3/32″ to 1-3/8″ outer diameter (O.D.), making it versatile for various applications.
CRD410 Manual Fitting Inserter
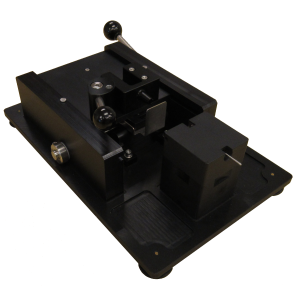
For those seeking the control and flexibility of manual operation, the CRD410 is an excellent choice. This inserter is designed to handle a wide range of fitting tasks with precision.
Key Features:
- Versatile Jaws: The CRD410 can be equipped with different jaw types to suit various tubing and fitting combinations.
- User-Friendly: Designed with ergonomics in mind, this manual inserter is easy to operate, reducing the risk of operator fatigue.
Applications of Fitting Inserters
Fitting inserters from Clean Room Devices are used in a variety of industries, each with unique requirements and challenges. Here are some examples of their applications:
- Medical Device Manufacturing: Precision is crucial in medical device manufacturing. Ours ensure accurate and reliable installation in flexible medical tubing, meeting stringent quality standards.
- Automotive Industry: In the automotive sector, fitting inserters are used to assemble components that require precise connections, such as in fuel lines and air conditioning systems.
- Water Purification Systems: Manufacturers of water purification equipment rely on fitting inserters to ensure secure and leak-proof connections in their systems.
Enhancing Cleanroom Efficiency
Using advanced fitting inserters in cleanroom environments offers numerous benefits that contribute to overall efficiency and productivity. Here’s how:
- Improved Accuracy: Automated and semi-automated fitting inserters reduce the risk of human error, ensuring that they are installed correctly and securely every time.
- Increased Speed: These devices significantly speed up the installation process, allowing for higher throughput and meeting demanding production schedules.
- Reduced Labor Costs: By automating repetitive tasks, fitting inserters reduce the need for manual labor, lowering operational costs and freeing up staff for more complex tasks.
- Enhanced Safety: Ergonomically designed inserters minimize the risk of repetitive strain injuries, creating a safer working environment for operators.
Conclusion
Fitting inserters are indispensable tools in cleanroom environments, providing the precision, efficiency, and reliability required in various industries. At Clean Room Devices, we offer a comprehensive range, including both semi-automatic and manual models, to meet the diverse needs of our clients. By investing in advanced fitting inserters, businesses can enhance their cleanroom operations, improve productivity, and maintain the highest standards of quality.
Explore our range of fitting inserters and discover how Clean Room Devices can help you achieve optimal efficiency in your cleanroom operations. Contact us today to learn more about our products and services.